Robot Vision
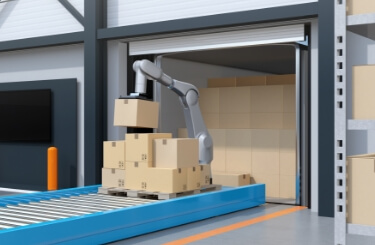
Robotic Automatic Picking System for Logistics Industry
MicroTechnica’s latest image processing technology, which combines conventional 3D imaging technology and 2D image processing with a learning algorithm based on Deep Learning, significantly increases the recognition rate for irregular shapes and random workpieces even without product registration.
AI-driven Box Depalletizing System
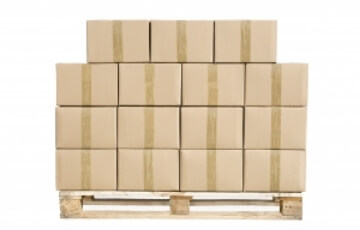
Robots unload boxes from the pallets and cage carts. This system can handle random workpieces and can recognize almost all types of boxes, such as those with and without PP band, and those with black or clear tape.
With the installed vision system, it's able to recognize the 3D position of individual boxes stacked on the top to determine picking points.
AI-driven Bag Depalletizing System
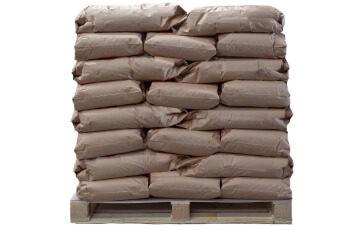
Robots unload bags and similar items from the pallets. It can recognize thin and unstable overlapping bags or plain, no-pattern bags.
Its vision system enables automatic depalletizing of bags with robots..
Piece Picking
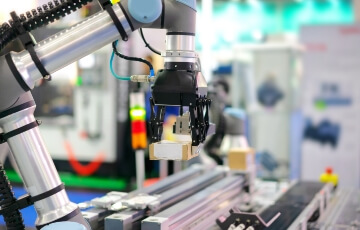
For better image recognition of small workpieces such as small carton boxes, we employ new 3D image recognition technologies which combines conventinal 3D and 2D method and a DeepLearning learning model in addition to traditional template matching.
Mech-Eye Robot Vision
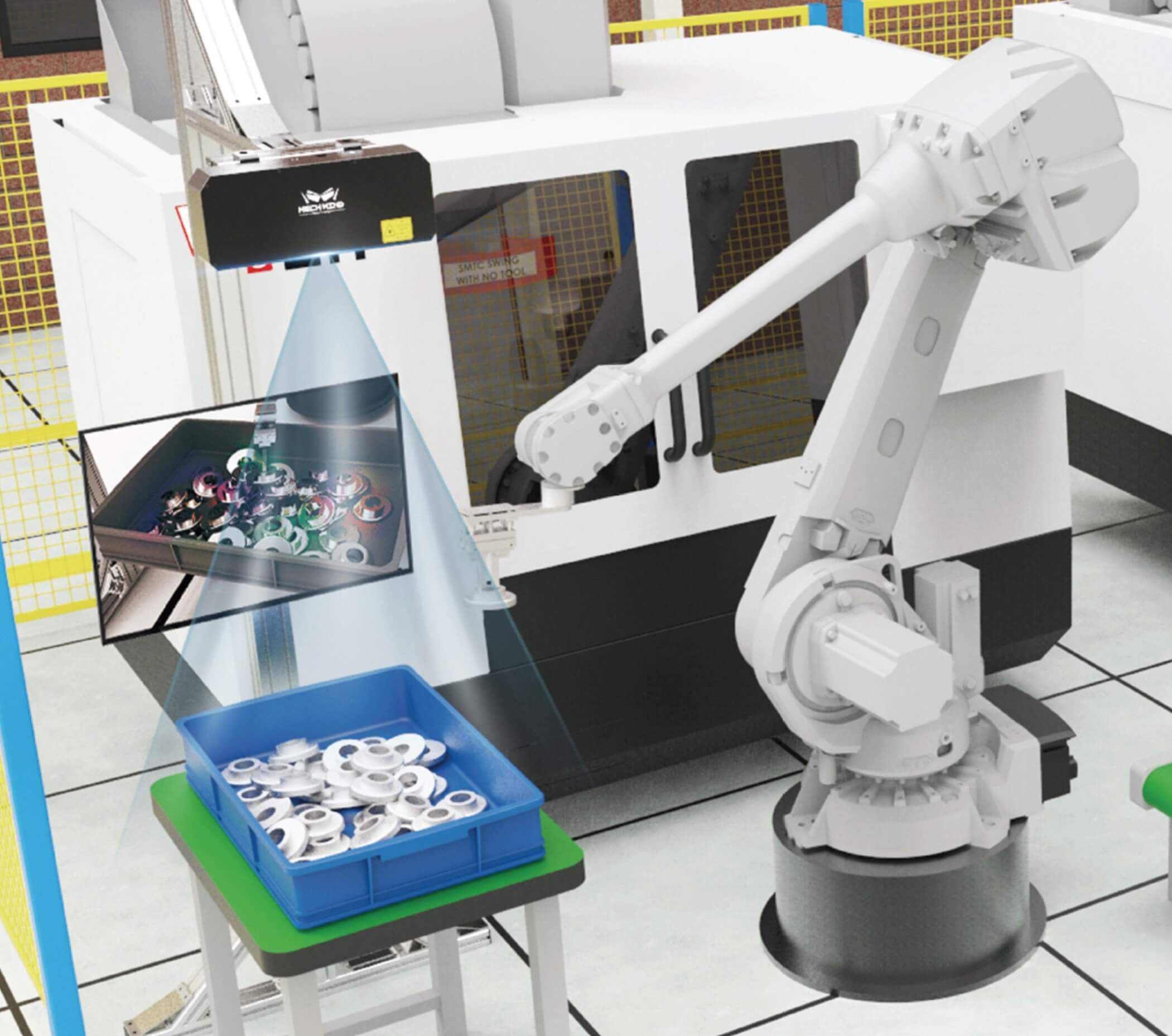
Achievements and Technological Advances of MicroTechnica's Robot Vision for Depalletizing
2019+
The Development of a New MOP (Mathematical
Optimization) Algorithm for Box Recognition
Recognition of boxes that are all in one shape and on a single layer at high speed without a need for pattern registration!
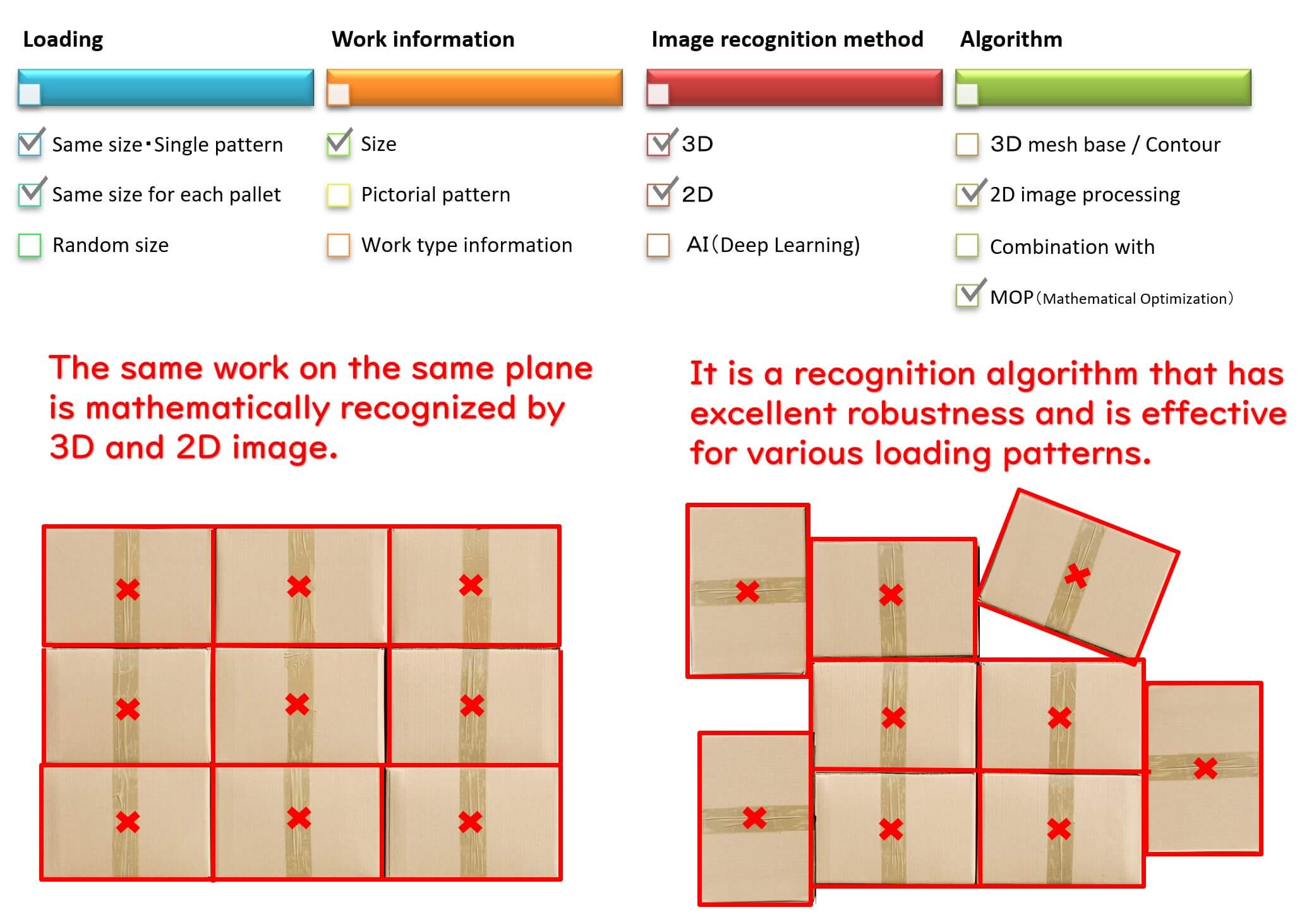
2016-2018
Improved Learning-Based Recognition through the Combined Use of 3D and AI (DeepLearning)
By implementing AI, it is now possible to recognize almost all boxes in a mixed state!
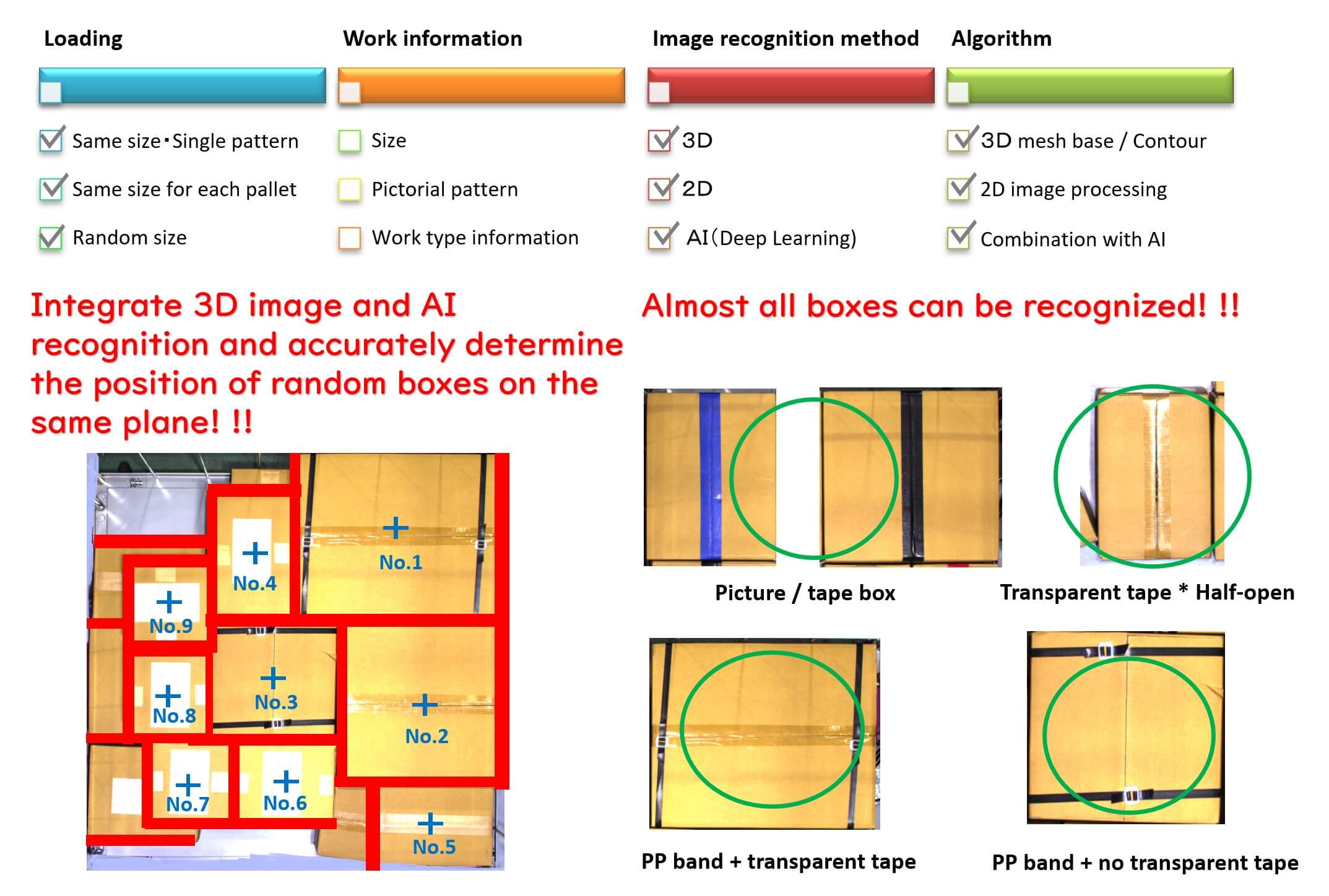
2015–2016
Improved Recognition Accuracy Through the Combined Use of Point Cloud Information of 3D Camera and Color Image
Using a 3D camera makes it possible to measure the shape of the top surface of boxes more accurately and at high speed, and using this in combination with a 2D color camera as well as by using contrast successfully resulted in improved box division accuracy.In addition to standard depalletization software, we implemented new robot calibration software for multiple 3D cameras and various robot manufacturers as well as a hand interference check function.
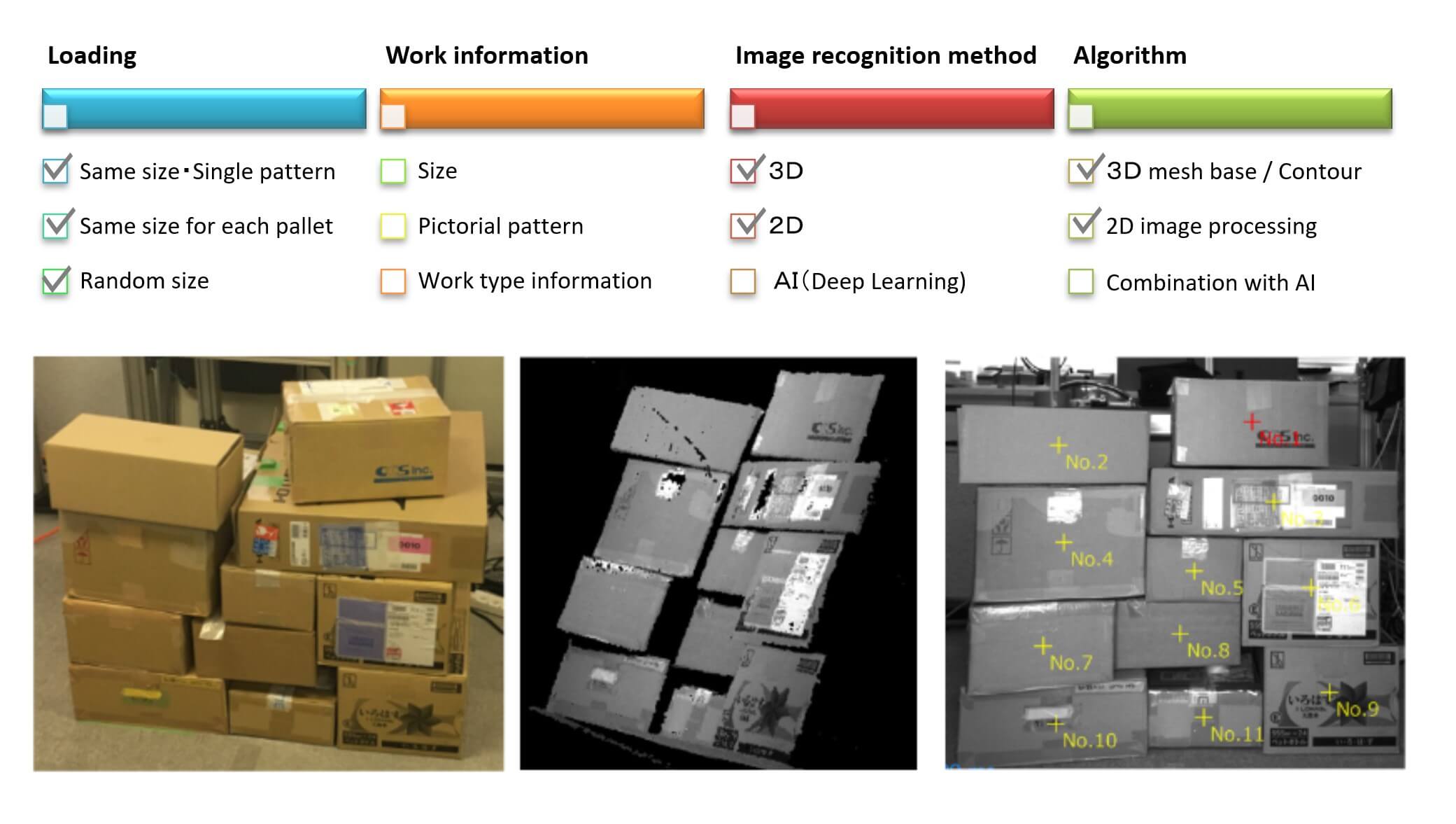
2014–2016
Color Image Processing Added to Point Cloud Processing for Bag Recognition
Unlike boxes, the boundaries (edges) of individual bags have gentle peaks and valleys. We achieved the commercialization of bag recognition by creating a mesh on a very small plane, setting the difference between normal vectors as the boundaries, and recognizing each bag in combination with segmentation and contrast.
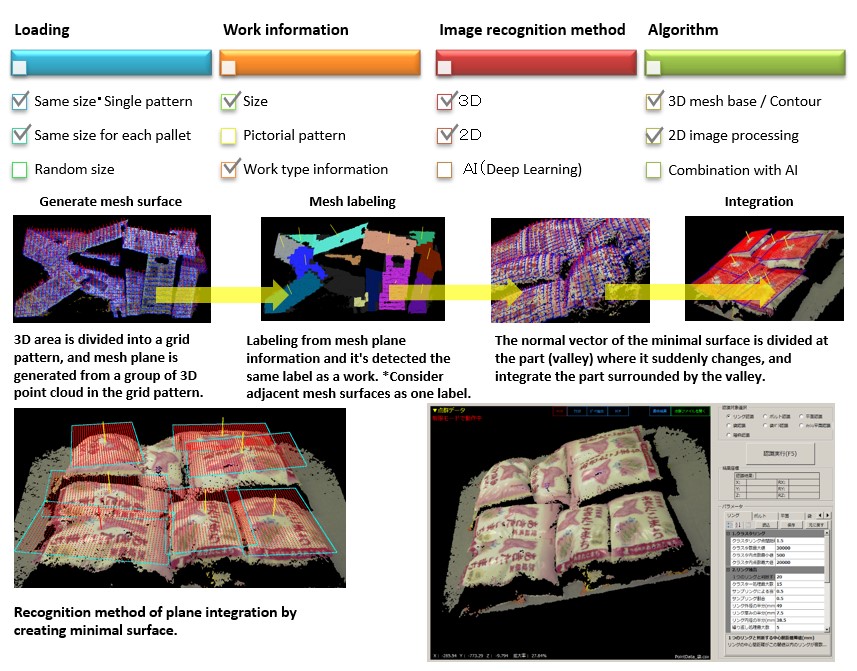
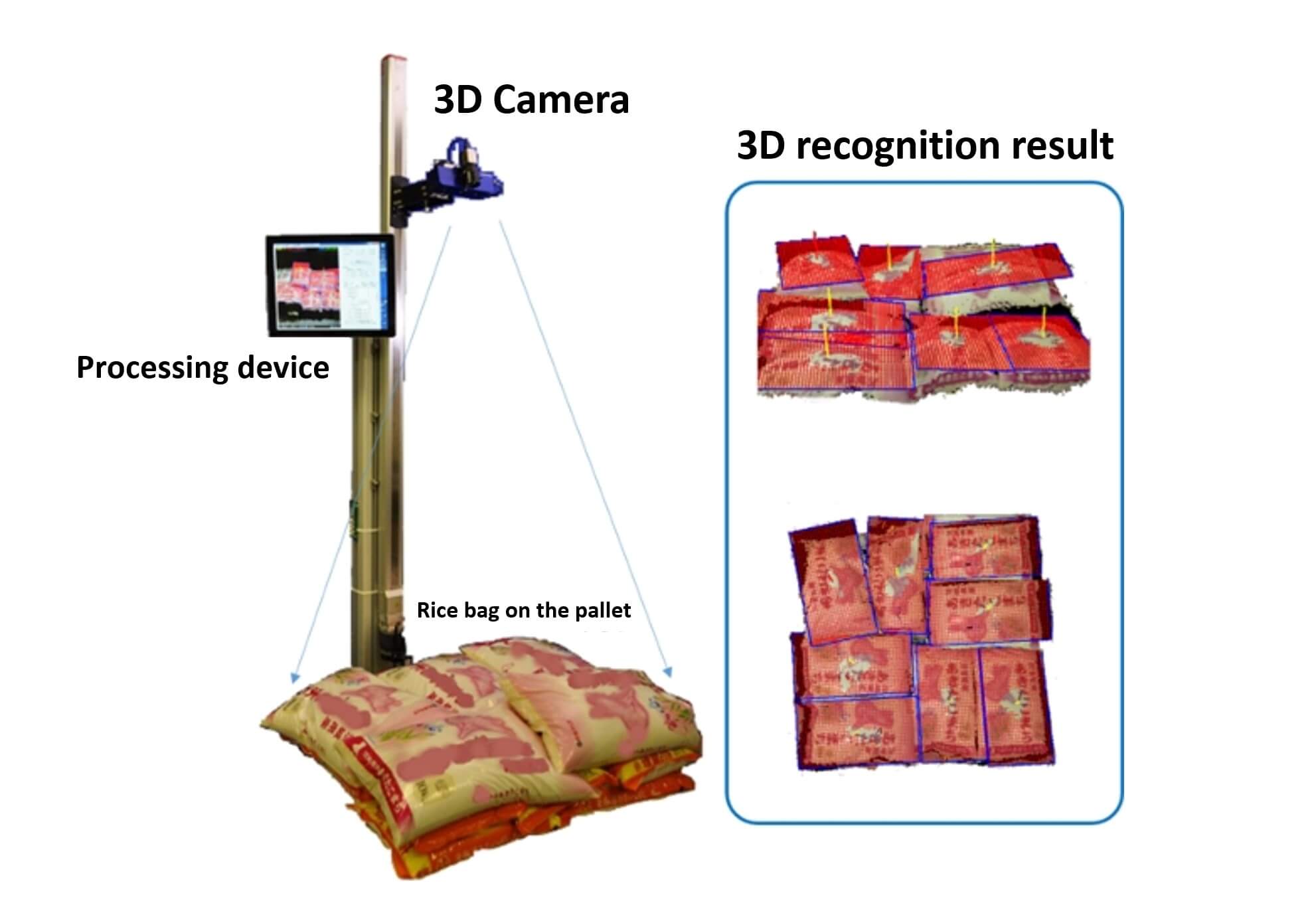
2013–2015
Improved Accuracy with Contrast Imaging
As a method of recognizing the condition where there are multiple boxes on the same plane, there is almost no difference in height, and there is almost no gap between boxes, we adopted a method of dividing the boxes on the same plane by utilizing the difference in contrast.
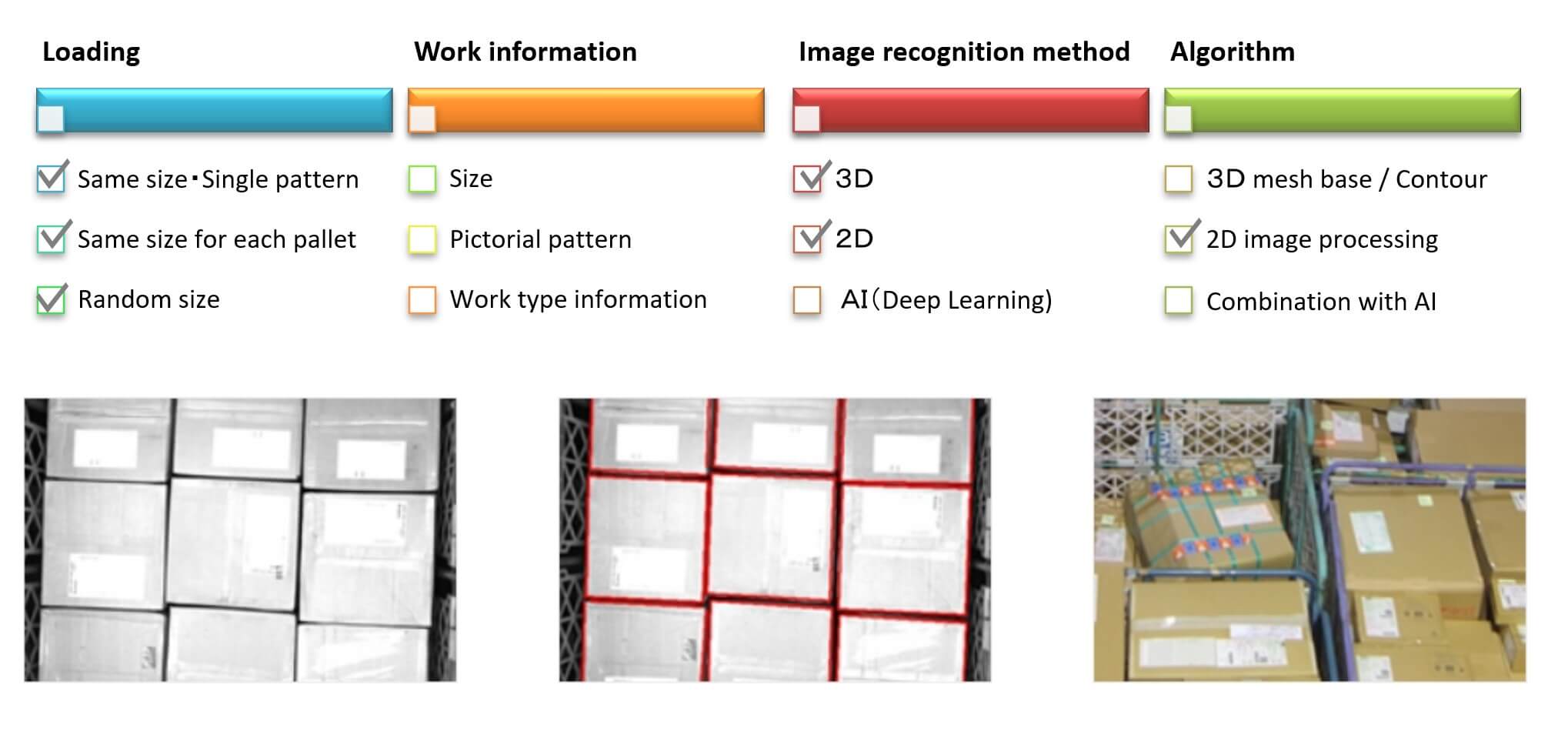
2010–2013
Combining the Use of a Grid Laser and a Stereo Camera
We delivered the world’s first robot vision for box recognition that supports random workpieces!!
Imagine a situation in which there is an infinite variety of boxes that are loaded randomly on pallets or cage carts, and you have no prior information on the types of boxes that are there. “How would you conduct image recognition?”
This is the challenge our company began to take on in 2010. If you know the type of boxes being used and have information about the size and print pattern design of the boxes in advance, it can be relatively easy to recognize the individual box by using something like standard two-dimensional image processing template matching. However, in a situation where you have no prior information and you don’t know what has been loaded, how you accurately recognize individual boxes is key. In 2010, the performance of the device known as a 3D camera was inferior to that of today, but through trial and error, our company developed a method for conducting 3D measurement by combining a grid laser with a stereo camera, and introduced this method to a major distribution center.
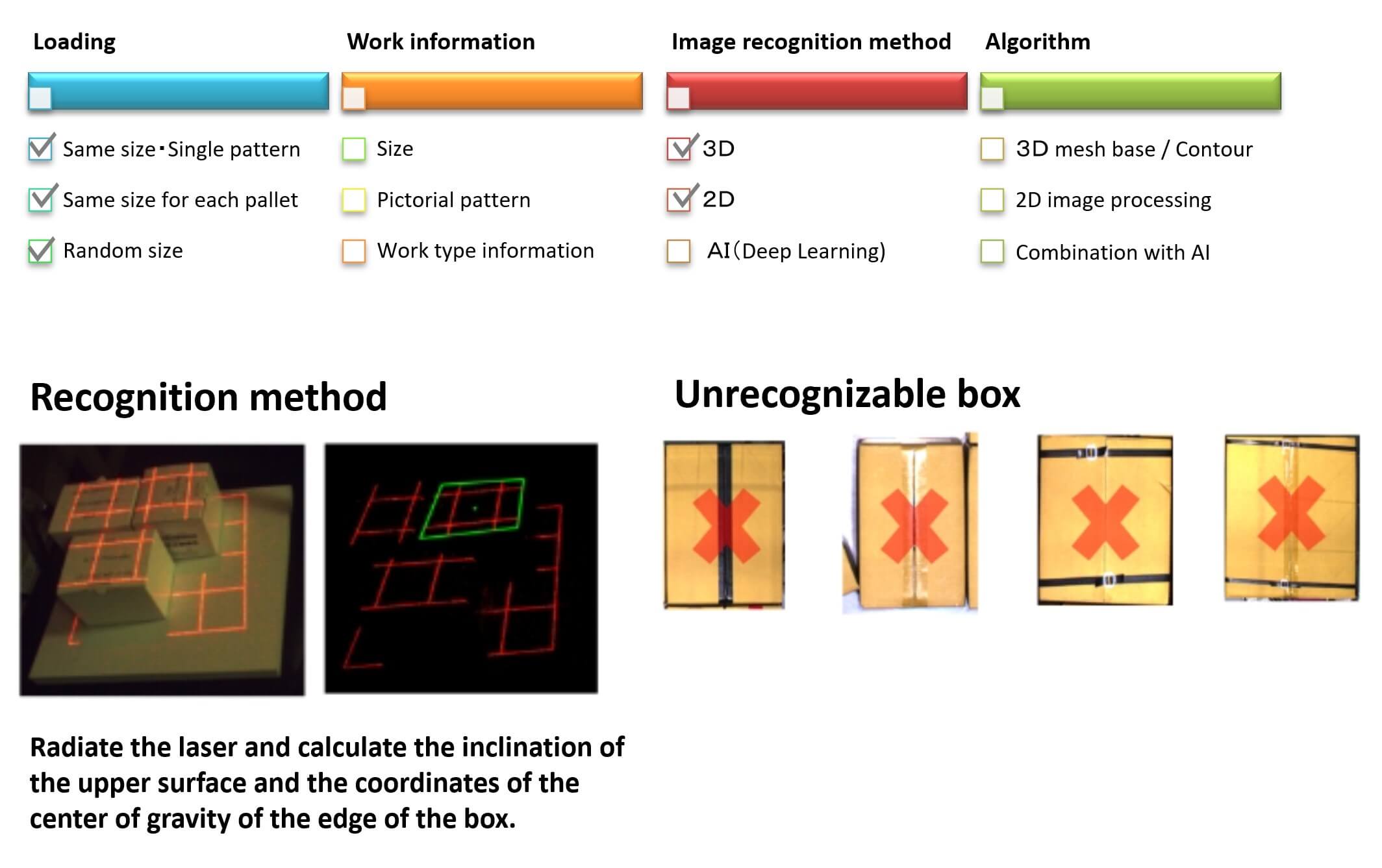
A Volume Calculation Unit for Boxes
This unit accurately measures the length, width, and height of workpieces such as boxes and other items on conveyors.
It can measure height by freely setting the reference plane, and it instantly takes measurements that are essential for automatic palletizing, including the area of the top surface, inclination, and center of gravity coordinates.
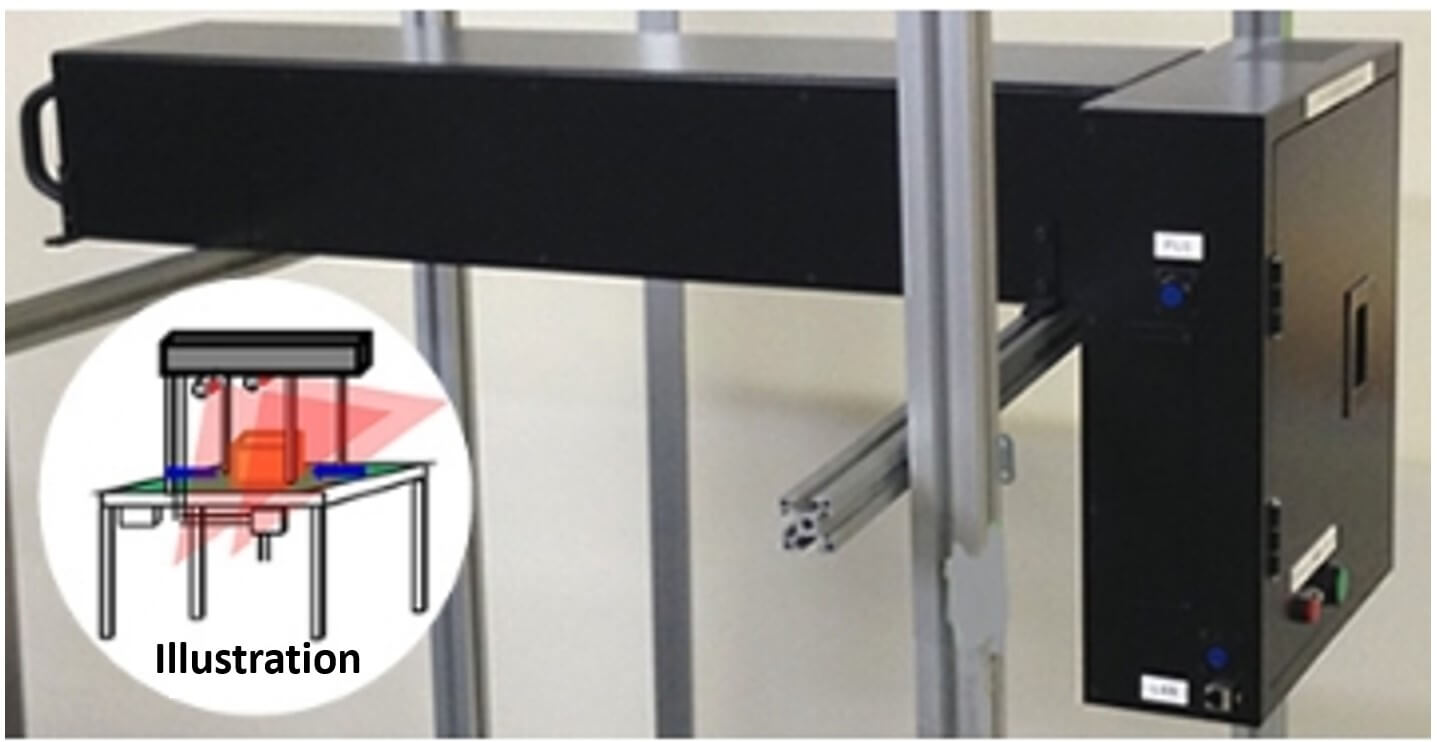
Features
- No need to register box shapes!
- Easy to connect with multi-joint robots
- Measurements:
Top surface area and top surface height, length, and width center of gravity coordinates, volume, and rotation angle of top surface (θ) - Measurement time: 1 second or less
- Can conduct measurement even when cardboard boxes are tilted
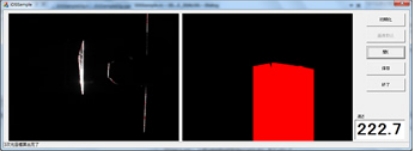
Measuring height
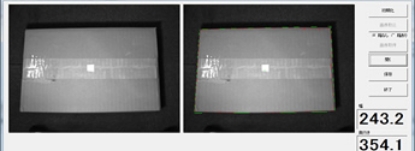
Measuring width and length
Please feel free to contact us if you have any questions.
Contact Us
Feel free to contact us with any questions or concerns
Contact Us